Aircraft Building Techniques
An overview of various methods of aircraft construction.
Custom-built aircraft come in all shapes and sizes. Many different materials can be used, and each aircraft will have its own particular construction techniques. There is no "perfect" construction method - each has various advantages and disadvantages, but the end goal is the same - an airworthy aircraft.
Choose whichever construction technique appeals to you and you feel comfortable using.
Wood and Fabric
By far the oldest construction method, well proven over time. Materials availability is high, with the tooling required generally ordinary carpentry tools.
Construction can use solid plywood panels, or built up longerons and frames etc made from solid timber. Normally wooden components are glued together using modern epoxy adhesive. Some glues require temperature controlled environments, so in cold climates you may need to heat your workshop.
Wooden structures are commonly covered with a shrunken fabric to provide a weatherproof outer layer. This fabric can sometimes form the outer skin of the aircraft without any timber layer underneath.
Examples: Jodel Series; Corby Starlet; Minicab; Maranda
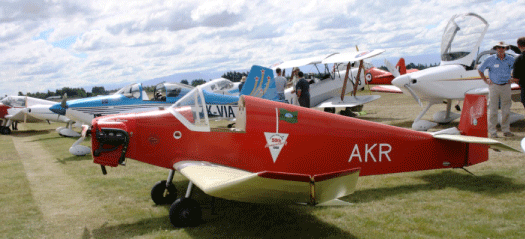
Jodel D9
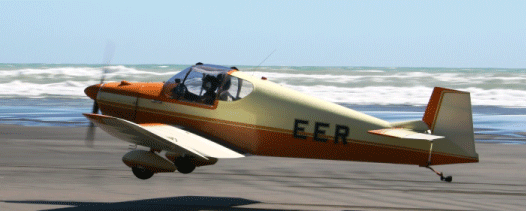
Jodel D11
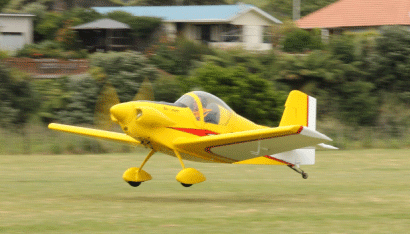
Corby Starlet
Tube and Fabric
Steel tube framework is often used for fuselages, a technique very common on older factory built aircraft. The steel used is a very strong yet light Chrome-Molybdenum alloy.
Some kits come with steel tube components pre-welded, or at least tacked together. Where frames are not supplied pre-welded, you will require the appropriate welding plant. Adequate welding ability is essential to achieve the necessary high quality welds.
Arc welding normally proves unsatisfactory and while gas welding can be used, TIG equipment achieves the best results.
Tube fuselages are often fitted with wood or Aluminium stringers or fairings, then covered with shrunken fabric, in the same way as wood and fabric structures.
Examples: Storch; Protech PT2; Kitfox; Avid Flyer; Pitts Special
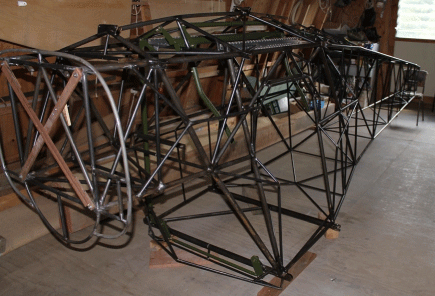
Storch fuselage frame upside down awaiting covering
Alloy Stressed Skin (Metal)
"Stressed Skin" refers to a metal structure where the skin itself takes some of the various structural loads. It does not require extensive internal framework, normally only using a series of cross frames and light stringers.
Along with riveting together the sheet aluminium alloy with solid rivets, additional strength is often obtained by folding the various panels so that the fold gives a certain amount of rigidity.
Stressed skin kits often come with the major panels cut, folded and even pre-drilled.
Plans built aircraft, or kits where pre-folding has not been done will require a suitable sheetmetal folder and forming blocks for curved surfaces.
Solid riveting requires an air hammer and a bucking bar – sometimes this task requires two people. There can be some awkward reaching inside confined spaces. Blind "Pop" rivets are not normally a suitable alternative unless specified on the plans by the manufacturer.
In New Zealand, the high strength alloy will corrode due to a maritime climate; therefore take special care to use corrosion resistant primers inside structures and around all joints.
It is relatively easy to learn the skills needed for this method. The construction time can be shorter compared to other methods, especially if using pre-formed kit parts.
Examples: Vans RV series; Thorpe T18; Murphy Rebel; Zenith Series
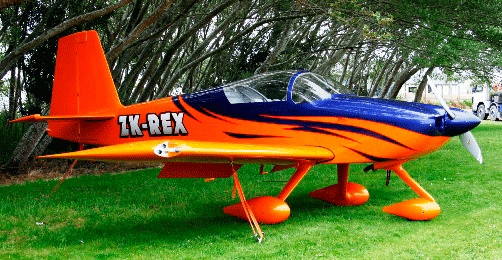
Vans RV7A
Composite Materials (Reinforced Plastics)
Traditionally "Composite" aircraft have been made from Fibreglass; however modern examples may include a number of new, exotic materials such as Kevlar, Nomex, Carbon Fibre and Graphite.
The more exotic materials are normally factory moulded by a kit manufacturer. In many ways such advanced kits resemble an unassembled plastic model kitset – but somewhat larger! The builder has to join the various pieces to together and finish the exterior surfaces etc. This can be quite precise work, and minor surface blemishes are very noticeable on such composites.
Older kits and plans-built aircraft are built up from blocks of foam cut and sanded to shape, upon which layers of fibreglass cloth and resin are built up – similar to a surf board. Sometimes plywood is used as part of the structure underneath.
Composite construction requires special resins and adhesives, most of which are hazardous to your health – always wear protective equipment. These resins also require precisely controlled temperatures to cure to the correct strength, so this is an important factor when preparing your workshop. With premoulded components, assembly can be quite quick, however a lot of time is spent filling and sanding.
The smooth surfaces mean these aircraft tend to be quite high performance.
Examples – Dragonfly; Long EZ; Lancair Series; Glassair; KR2
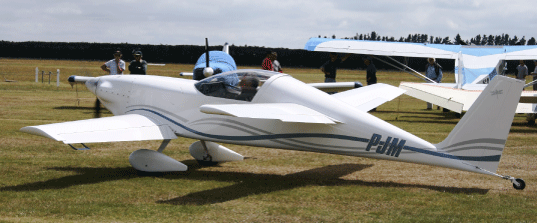
Dragonfly
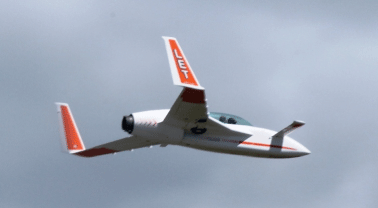
Long EZ (Jet variant)
Other methods
Other, less common construction methods include:
- Alloy tube – the structure is made of aluminium alloy tube, generally joined together by riveted flat alloy or steel plates known as "Fishplates". The structure is often fabric covered in a manner similar to a steel tube structure.
- Wood and Fibreglass – this method is similar to that used on some yachts, with a plywood structure built up, then given some shape and smoothness with a built up layer of fibreglass.